
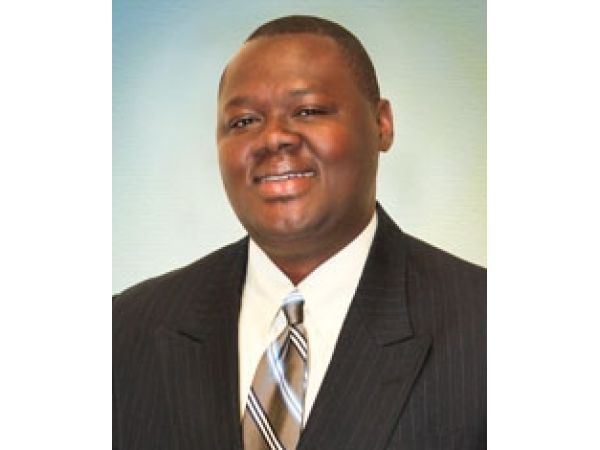
Next, various lean enterprise tools are discussed. The rest of the chapter will cover the following sections: First, a description of lean techniques is covered. It helps focus on improving material flow, information flow, and process quality of a business. The events often eliminate the need for costly overtime by improving processes while collapsing lead times, and dramatically reducing work-in-process. Furthermore, continued improvements will compound the return, since Kaizen never really ends (Mika, 2005). They are important because they provide an excellent return on investments of financial and human resources. This results in shrunken lead times, dramatic reduction in work-in-process, and reduction of scrap and defects, while minimizing the need for capital expenditures (Mika, 2005). During Kaizen events, worker’s ideas are highly encouraged for frequent and small improvements. These events help management to find new ways to gain substantial savings in time, space and labor output (Alukal & Manos, 2006). Kaizen events are ways of accelerating improvements to worker productivity. Ninety-four percent of manufacturing errors or problems belong to systems, and lean manufacturing attacks these systems with the common goal of cost reduction or improvement of production (Deming, 1986). Value-stream mapping of products was started through the Toyota production system of lean manufacturing. Harris and Donatelli (2005) stated that value-stream mapping is the foundational tool used by any company that is on the cutting edge of transformation from a traditional organization to a lean enterprise. The team focuses on continuous improvements and uses tools and techniques to identify and eliminate wastes. It uses a team focused methodology requiring knowledge to be pulled from everyone (from the hourly worker to the upper management), and driven by continuous improvement (Kaizen). Continuous improvement with a focus on the seven wastes is part of lean manufacturing. Taiichi Ohno classified these wastes into seven basic types: overproduction, transportation, process waste, operator movement, inventory, idle time, bad quality (Bateman & David, 2002). Source of wastes identified by Ohno include: errors that require recertification, product defects, process steps that are not needed, goods or employee movement without any purpose, goods and services that don’t meet the needs of the customers, and any waiting time due to bottlenecks. However, according to Soderquist and Motwani (1999), Taiichi Ohno was the first to present lean manufacturing to eliminate production waste at Toyota (Soderquist & Motwani, 1999). Lean process can be traced back to the early 1900s, when Henry Ford introduced the notion of mass production in 1913 (Miller, 2005).
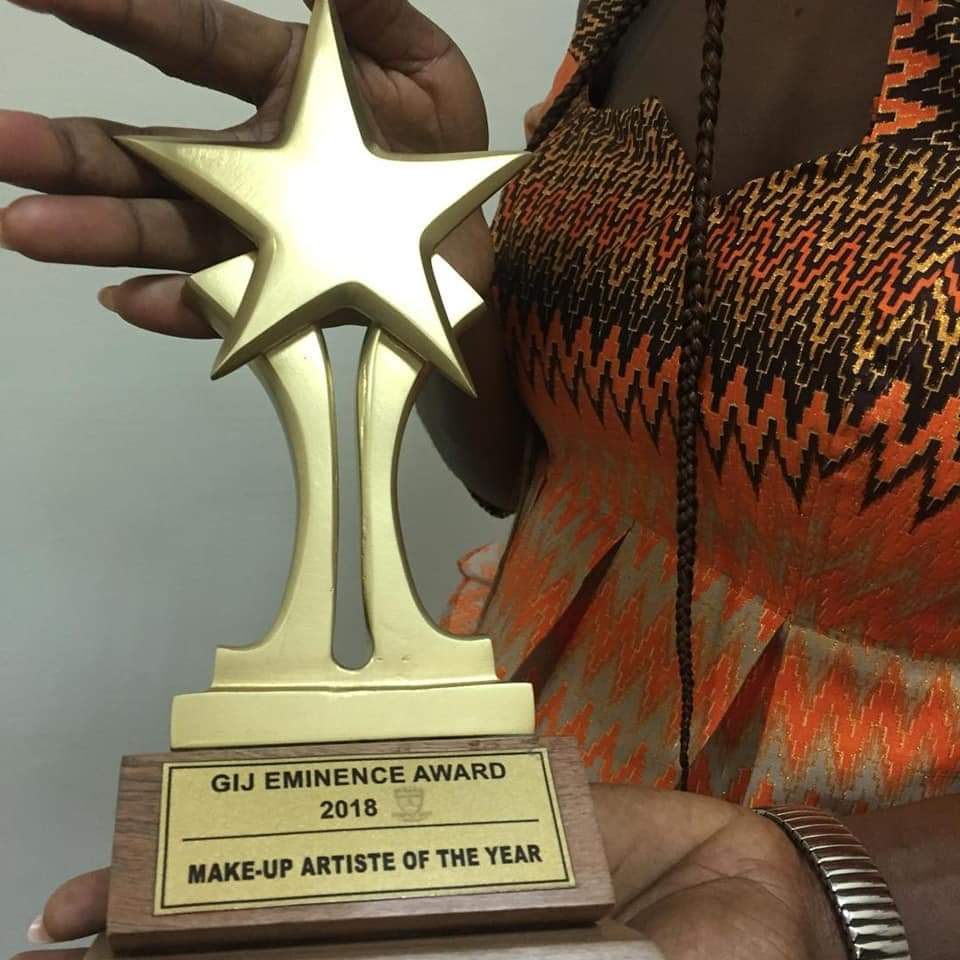
#Edem tetteh free
Lean manufacturing strives for continuous improvement towards an ideal through relentless reduction of waste, where ideal means delivering what the customer requests on time, on demand, and free of defects (Miller, 2005).
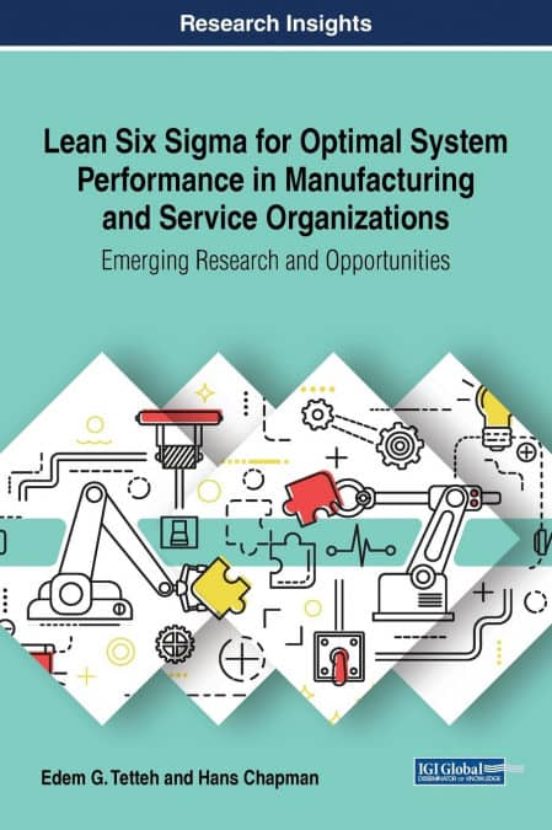

The goals are zero lead time, zero inventory, and zero defects, resulting in higher customer satisfaction (Tapping, Luyster, & Shuker, 2002). The philosophy of lean uses a process of waste reduction, thus producing higher quantity and better quality products with the least resources possible. Then, the idea was expanded by a research group at Massachusetts of Institute of Technology (Womack & Jones, 1996). The concept of lean started first with the Toyota Production System (TPS). Lean manufacturing has been shown to improve the competitiveness of organizations. The results support the criticality of metrics and their impact in implementing a lean manufacturing process in a global supply chain environment. The significance of the effects of these variables were assessed based on various lean supply chain factors such as First In First Out (FIFO), Setup Wheel System (SWS), Standard Operating Procedures (SOP), Clip System(CS), and Key Performances Indicators (KPI). Multivariate Analysis of Variance (MANOVA) was utilized to evaluate the performance of work cell, shift, worker’s experience, and kaizen event participation level during a lean enterprise deployment effort at a multinational organization. The technique is a vital strategy to increase productivity and effectiveness with respect to the movement of goods. Lean management is one of the key techniques businesses adopt in redesigning their processes. AbstractTo meet customer’s needs for high-quality goods and avoiding risks of product-liability, global firms continually evaluate the performance of their supply chain for optimum design.
